Batteries present a unique challenge when it comes to testing due to their distinctive coverage requirements. “You could argue that testing a battery is closer to testing a human body than testing a circuit board,” said Ben Wrightsman, CEO of BIC, during the NI Connect 2023 conference. “Batteries, like humans, are highly dynamic as their conditions change based on our usage in their environment and each one behaves a little differently.” Moreover, batteries come in a wide variety of form factors, sizes, chemistries, and capacities, necessitating test systems that are not only highly capable but also incredibly flexible.
To truly comprehend the inner workings of a cell to address quality objectives and ultimately minimize defects, more advanced measurement solutions are needed. The industry has traditionally relied on legacy methods of testing that can be characterized as highly manual, limited in coverage, and at the end of line. These methods ultimately provide insufficient insights and require significant testing time. To overcome these challenges and build better batteries, NI has developed a cell quality testing solution based on the modular PXI hardware platform and open software environments. By more accurately and comprehensively profiling the impedance of the cell, using techniques such as AC-IR, DC-IR, and EIS, this solution helps engineers better understand a cell’s behavior with more accuracy, at faster speeds, and in a smaller overall footprint.
However, advanced testing methodologies alone are insufficient. Scaling these techniques from the laboratory to the production environment poses its own set of challenges. Battery manufacturing can be a time-consuming process, spanning several days to weeks, with numerous steps that can introduce defects. The goal is to reduce manufacturing time from weeks to mere hours or days, while simultaneously minimizing points of failure. Achieving this requires a departure from relying solely on end-of-line testing. “By working with BIC, we’re researching innovative ways to test throughout the battery manufacturing process so we can find defects sooner and closer to where they’re being introduced,” shared Eli Kerry, EV Battery Strategy Lead at NI.
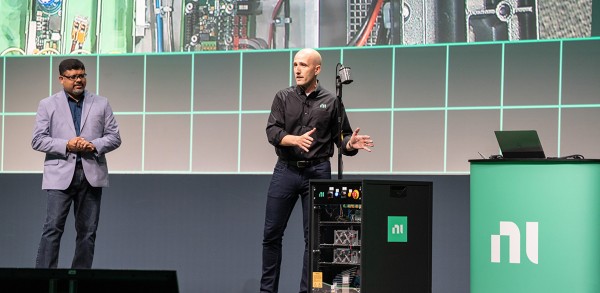
Eli Kerry, NI Battery Strategy Lead, highlights an NI battery cell testing solution at NI Connect 2023.
Given the scale of battery production, integrating widespread test and measurement capabilities becomes a complex undertaking. Thousands of test and measurement nodes are required, necessitating streamlined test asset management. Connected and smart test systems provide the solution, enabling effective orchestration, control, and management of all endpoints. This means that anyone within an organization, anywhere in the world, can access, manage, or update test assets. Leveraging connected systems, new test measurement techniques can be deployed, extracting valuable data across different manufacturing processes.
We’re researching innovative ways to test throughout the battery manufacturing process so we can find defects sooner and closer to where they’re being introduced.
—Eli Kerry, EV Battery Strategy Lead, NI
Ultimately, the key to building better batteries lies in the data produced and its value across the battery lifecycle. Battery manufacturers and OEMs are increasingly focused on harnessing the power of data, recognizing that it extends beyond the results of a single test. The true value lies in the comprehensive data obtained throughout the lifecycle of each battery and across all manufacturing activities. The utilization of this data through advanced modeling techniques allows manufacturers to better understand the characteristics of each battery cell. These evaluations are critical to improving yield and quality, and they pave the way for the next generation of high-performance batteries.
Through the collaboration between the BIC and NI, the path towards building better batteries is being forged.