As a leader in automotive testing, we’ve collaborated closely with customers who are working to overcome the challenges in the EV space, and we have gained a firsthand understanding of the ways that increasing demand and time to market pressures are directly influencing the battery test lab. One big problem that we’re seeing today is that everything is “scaling up” and becoming harder to manage.
Managing the Problems Caused by
Increasing Scale
In the past, a lot of the research that was being done, whether it was for batteries, inverters, or motors, was quite small scale—at least from an automotive perspective. What teams needed most was small-scale, flexible R&D equipment. While R&D is still happening, what we’re seeing now is a transition into more large-scale validation. As batteries are released at a larger scale, the problem in validation becomes the need to scale up, and that has a significant impact on the laboratory equipment you need.
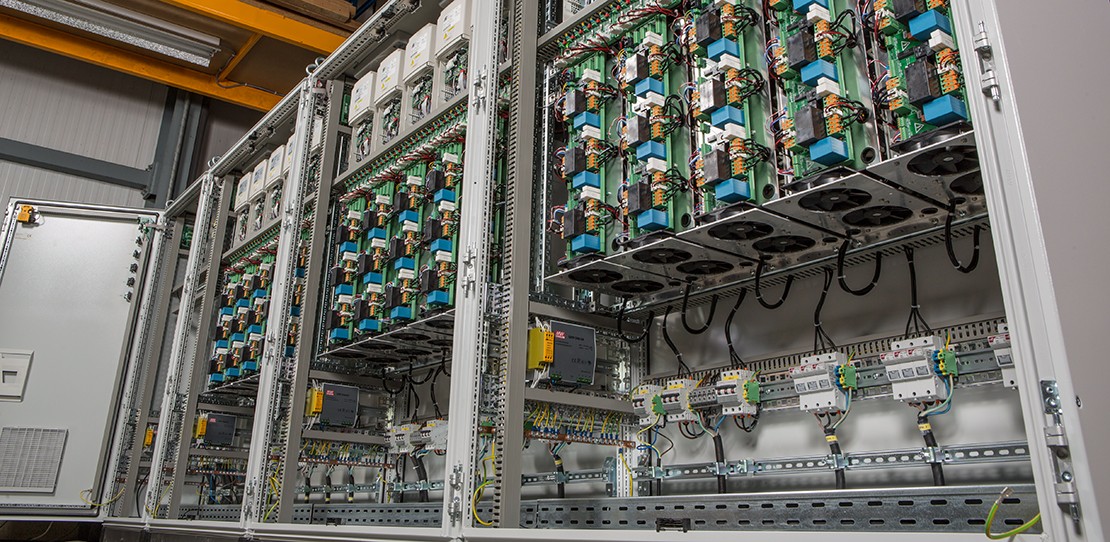
It's not just a problem of finding effective ways to test a battery. New problems emerge in the form of managing the lab, managing the power in the lab, managing all the equipment in the lab, and managing all the data that is being produced.
As testing in the lab increases, teams then can begin to see problems with managing variation across the testing lifecycle. For example, if you’re managing three test channels with their own ways of behaving, that’s manageable enough. But when you start to have hundreds, or maybe even thousands, of channels to manage, you might begin facing a fleet management problem—especially if your team rolls out changes to test programs for an entire fleet of test cells.
In other words, it’s as if you were trying to manage a team of hundreds of people who all speak different languages. You would have to take extra steps and use translators and ensure you’re standardizing the messaging protocols across multiple languages—it would be a very complex task to synchronize them.
The Current State of Power Electronics
One of the first decisions that gets made in the lab is how to supply power for large, and often very expensive, batteries and the equipment and infrastructure surrounding them. Because this is the first decision that gets made, teams might inadvertently constrain themselves as they’re forced to adapt everything in the lab to their power equipment. Additionally, teams must navigate how to best manage the power necessary to make changes at a large scale when needed without jeopardizing lab equipment and the power grid.
Today, the norm is to have solutions and equipment that directly feed off AC grids; however, as we look toward the future, that norm may present challenges. Consuming a lot of power directly from the power source of all the equipment in your lab creates a strain that demands better power distribution management. Future states will most likely include having controlled interfaces that take power from that AC grid and move it to DC, distributing DC power to multiple cyclers to effectively manage power in large-scale battery cycling facilities.
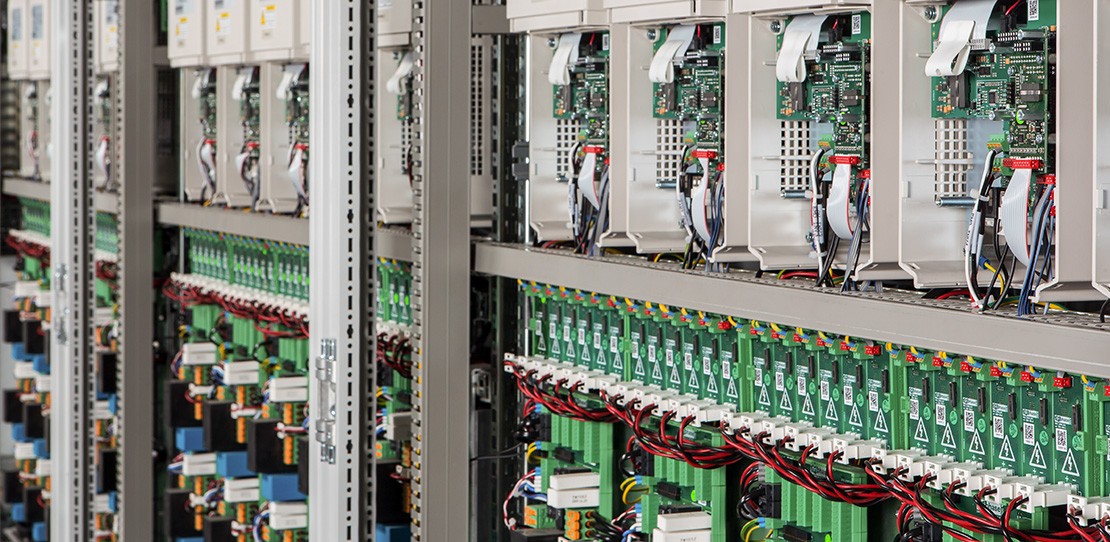
It may sound like a daunting challenge to solve, but there are ways to strategically approach this dilemma. We’ve worked with teams and engineers to solve these kinds of problems. For example, NI Power Electronics are designed with a controlled interface that uses a DC microgrid to distribute power within the facility. In fact, through Kratzer Automation, we’re already successfully leveraging these solutions to optimize power consumption and distribution.
Solving Software Challenges at Scale
We’ve navigated the conversion between AC and DC well, but when it comes to doing it at a larger scale quickly and safely, software must be addressed just as much as hardware. When large-scale management of test, equipment, and data makes teams inefficient, it becomes a software problem.
Another way to look at this problem is to imagine your team oversaw managing traffic on the road. Even the smallest miscalculation could be catastrophic. Synchronization, and in our case, software specifically is the key to success.
How do we go about solving these complex challenges? There are a few steps we can take:
1. Make sure every cycler that is connected to the network speaks the same language.
2. Prioritize synchronization and ensure alignment across the testing process.
3. Support processes by maintaining a scheduling mechanism.
This last point is a focus of NI Battery Test Systems, which aim to align everyone on what is expected of them and when, so you can easily coordinate teams.
After these areas are standardized and a centralized element holds every piece of the test process accountable for timely functions, conflicts can be mitigated or avoided entirely. Optimizing equipment and test communications and standardizing processes across teams also directly improves the process of gathering data and making impactful, data-informed decisions.
Small Steps for Big Impact on Test Team
Productivity
The problem is not whether we can solve these problems since there are multiple ways to approach these challenges. The problem is how can we approach these challenges in a way that enables our customers to be successful and increase productivity at the same time. We aim to make things easier for customers, whether that’s helping them focus on ensuring everything is consistently reported or having harmonized data formats to save time when comparing and analyzing data.
These problems are deceptively hard to solve, but it’s important to keep in mind that we lose the most time in the small areas. When we think of battery analytics, for example, we might think of an engineer working to solve complex machine learning challenges. But the reality is that everyday challenges are often more about ensuring all the equipment works harmoniously and does what it is supposed to do without wasting too much time. Or, on a different day, trying to get valuable data from tests that will lead to actionable insights and working to compare data that comes from multiple sources.
These steps may sound small, but often these areas are roadblocks preventing engineers from trying new things and being productive. At NI, we want to significantly reduce the time spent working through small everyday challenges so that our customers can spend more time focusing on big picture questions and Engineering Ambitiously.
Learn more about optimizing your battery validation lab with NI's software-connected solutions